Vacuum Forming Molds
All vacuum forming projects involve a mold. Due to vacuum pressure, heat, and demolding, V.F. molds will be subject to immense stresses. We know how different materials perform and exactly how a mold must be made in order to produce as many parts as possible as efficiently as possible. A poorly-designed mold will severely impact production time, cost, and mold-surviveability.
When only a few simple parts are needed, a hand-built MDF or carved foam mold will suffice, oftentimes with a skin to ensure smoother parts. However, for higher quantities or detailed molds, we use urethane, heavy foam or tooling board, fiberglass, or even aluminum. We know which materials to use for which kinds of projects. If you prefer to make their own molds to reduce costs, please call us before you start on your mold, our insight and experience will save you time and money. Better yet, avoid the headache and let us make your molds for you.
Urethane Molds
The urethane resins we use for molds are extremely hard, withstand high temperatures, and are capable of providing hundreds of parts. The process involves taking a printed or machined "master," taking a silicon mold, then casting the urethane out of the silicon.


Foam Molds
CNC machined (or ever hand-carved) foam is a faster and cheaper alternative to urethane. The number of parts required will dictate the density of the foam used (4lb-72lb) and the production material will dictate the secondary finish required, i.e. poly-prime, skin, etc.
Aluminum Molds
When you need hundreds of parts or absolute perfection, a CNC-machined aluminum mold is your answer.


Fiberglass Molds
During normal vacuum forming, the plastic is pulled over a positive mold. However, when the part is very deep or requires perfect detail, a negative mold is required. These can be made using a variety of methods, but require special expertise.
MDF Molds
When you need parts by the thousand and each one needs to be perfect, a CNC-machined aluminum mold is your answer.
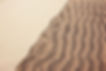

Negative Molds
During normal vacuum forming, the plastic is pulled over a positive mold. However, when the part is very deep or requires perfect detail, a negative mold is required. These can be made using a variety of methods, but require special expertise.